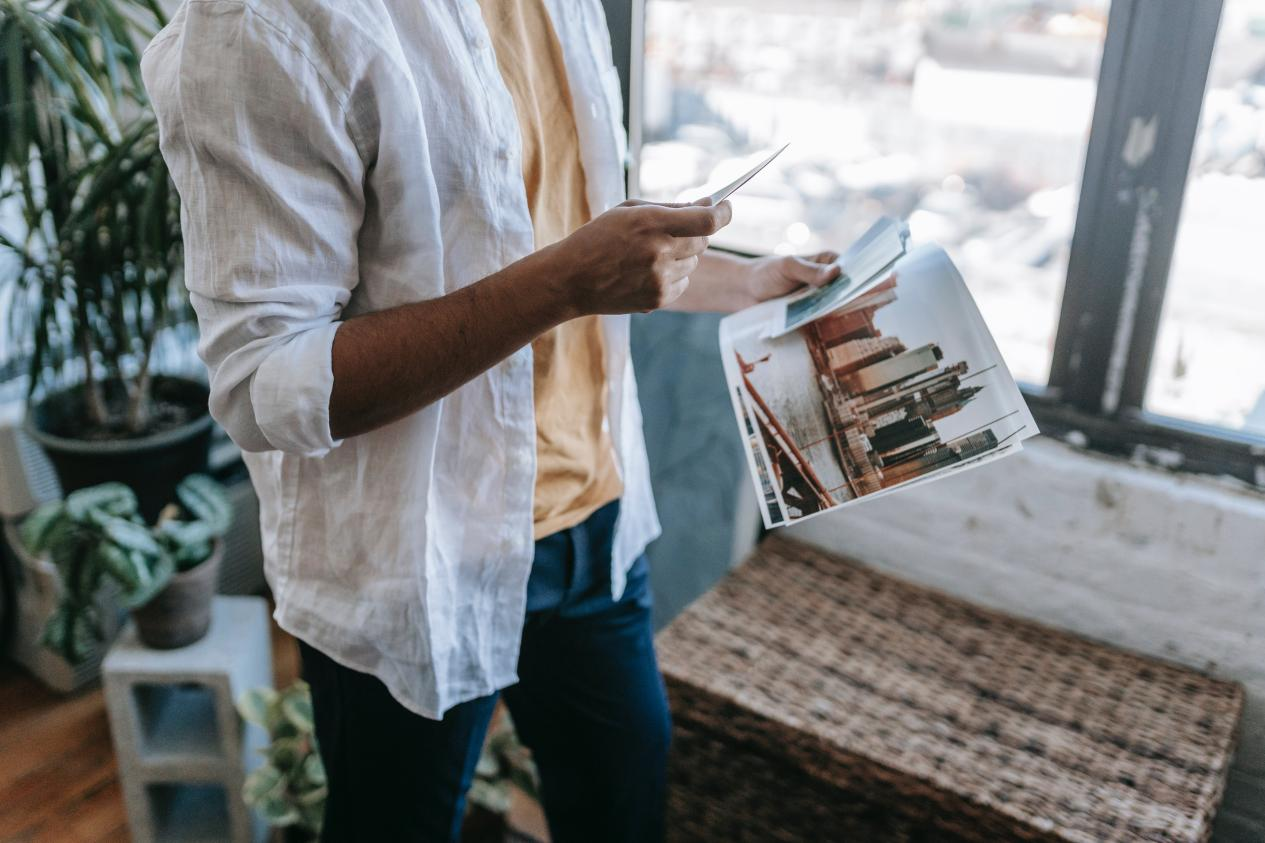
How to Effectively Manage Photo Paper Inventory?
●Predict Demand to Plan Procurement
Accurately forecasting photo paper needs is crucial for cost-effective inventory management. Analyze past sales data to identify trends by paper type, size, finish etc. Factor in upcoming events and projects that may increase demand. Optimize reordering levels and order sizes to maintain sufficient stock without over-investing in surplus inventory. Communicate regularly with paper suppliers to ensure reliable stock availability.
●Optimize Storage to Save Space
With different sizes and volumes of photo paper, storage is a challenge. Proper organization maximizes your storage footprint. Sort papers by finish, size and quantity per box for easy retrieval. Keep specialty papers readily accessible while racking bulk items more densely. Consider wall-mounted or overhead racks to store boxed paper vertically and free up floor space. Rotate inventory regularly so older stock sells before expiration dates. Protect paper from dust, moisture and damage by sealing bags, boxes and shelves.
A well-managed stockroom also boosts efficiency. Categorizing papers into clear sections organized by attribute streamlines the picking process. Label each location to aid workers in restocking and fulfilling orders promptly. Monitor inventory levels daily using systems like barcode scanning so you never run out of popular items. Schedule routine physical counts to reconcile records and identify any discrepancies.
Optimize further by outsourcing storage of seldom-used papers. Partner with a third-party warehouse provider near your studio to store specialty or seasonal items off-site until needed. This frees up valuable real estate in your facility. With the right inventory forecasting, organization and monitoring procedures, you can maintain ample paper supplies while minimizing storage space and risk of waste. Proper photo paper stock control is key to serving customers seamlessly.
How to Prevent Photo Paper Curling?
●Choose Appropriate Mounting for Different Thicknesses
Thinner papers are more prone to curling after printing due to moisture warping the sheet. For thin glossy or luster papers under 250 gsm, mount dry onto foamcore, gatorboard, or PVC-free poster boards using spray mount adhesive. Heavier papers 300 gsm and up can be directly taped or pinned onto rigid boards. Avoid stapling or using glue dots which may damage the print surface over time.
Metallic and textured papers need extra support. Lightly spray the print with removable adhesive and sandwich it between two foamcore boards for stability. Reinforce further by taping down the edges and corners. When framing behind glass, use acid-free foam mounting tape all around so the backing holds the shape perfectly flat without pressure points.
●Control Temperature and Humidity Environments
Curling most often occurs in high humidity conditions as the moisture gradient causes uneven drying. Be especially vigilant during seasonal shifts. Keep printed photos flat overnight in low-humidity storage before mounting or framing. Maintain a humidity level between 30-50% to properly condition photo papers and prevent warping.
Similarly, temperature swings can impact paper as it expands and contracts at different rates than surrounding materials. Store paper flat in a climate-controlled space to minimize dimensional changes from extreme hot/cold exposures. For displays, choose frames constructed from materials that allow air circulation but distort minimally from temperature fluctuations.
Following these techniques - choosing appropriate mounting or framing for the paper caliper combined with humidity and temperature control - helps counter the natural forces pulling fibers out of shape. With careful handling after printing, studios can deliver flat, crisp images that maintain their museum quality for clients.
How to Prevent Photo Edges from Fading?
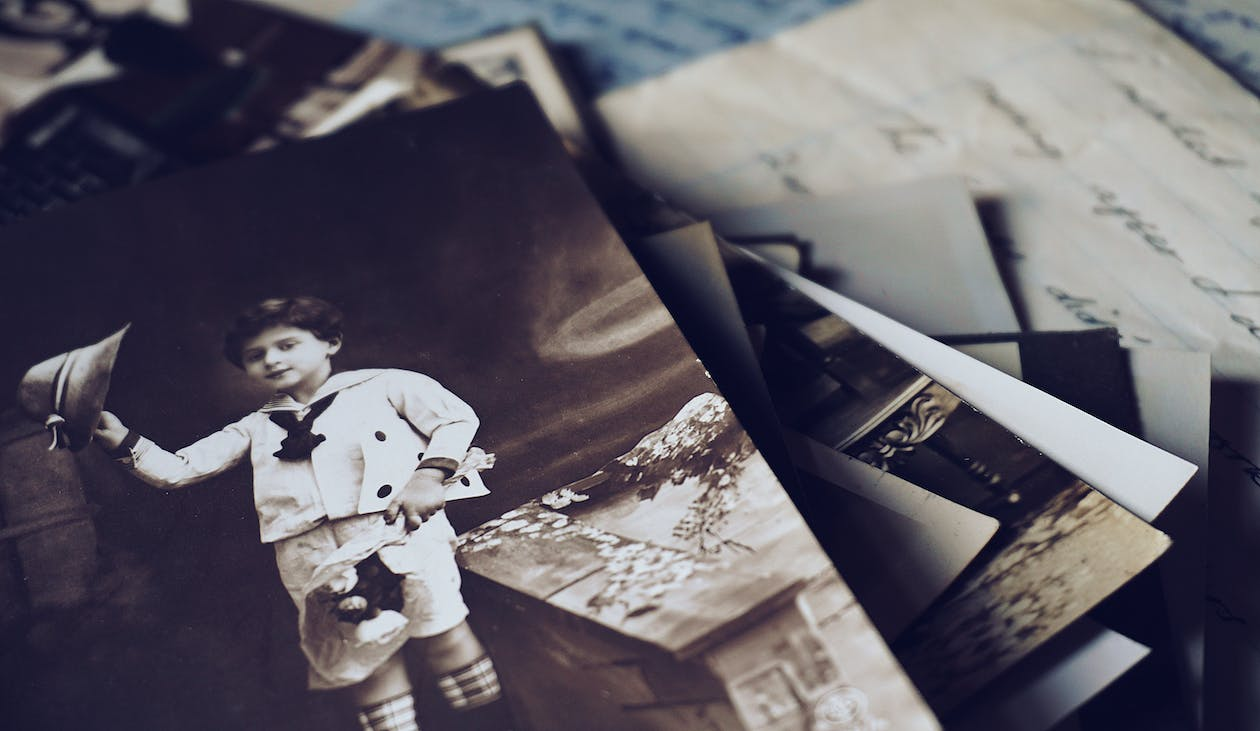
●Optimize Settings for Different Printing Methods
Inkjet printed edges are prone to dye degradation from oxidization if not properly sealed. For inkjet prints on photo paper, enable any available “borderless” or “border extend” functions in printer settings. This deposits tiny droplets of ink at the edges to blend colors seamlessly to the paper border.
Thermal and dye-sublimation printers require different approaches. Test printing small images with a 0.25-0.5cm perimeter of color behind the photo edges. The outward-printed “mask” protects sensitizing dyes near the border from environmental damage over time. Take test prints to determine the optimal protective margin size for each paper type.
●Detailed Edge Treatment Techniques
For all print methods, immediately post-process edges to safeguard colors and prevent fading. Use a dense fusain graphite pencil or soft micro-tip marker to gently color the perimeter. Blend the graphite evenly around each side without touching the image area.
Alternatively, apply a thin coat of clear acrylic sealer spray specifically formulated for photo edges. Lightly mist the border from 12 inches away to avoid drips. Allow both graphite and sealer to fully dry before handling prints.
When mounting or matting, leave a small revealed margin between the matte cutout and printed border. The protected “pocket” prevents light exposure and physical abrasion that causes edge degradation. Opt for non-UV glass in frames and avoid direct sunlight display to further prolong border colors over time.
With optimized printer settings and careful post-printing sealing, Photo Labs can deliver prints with long-lasting, vivid borders that maintain image integrity for clients year after year.
Why Photo Quality Varies on Different Photo Papers?
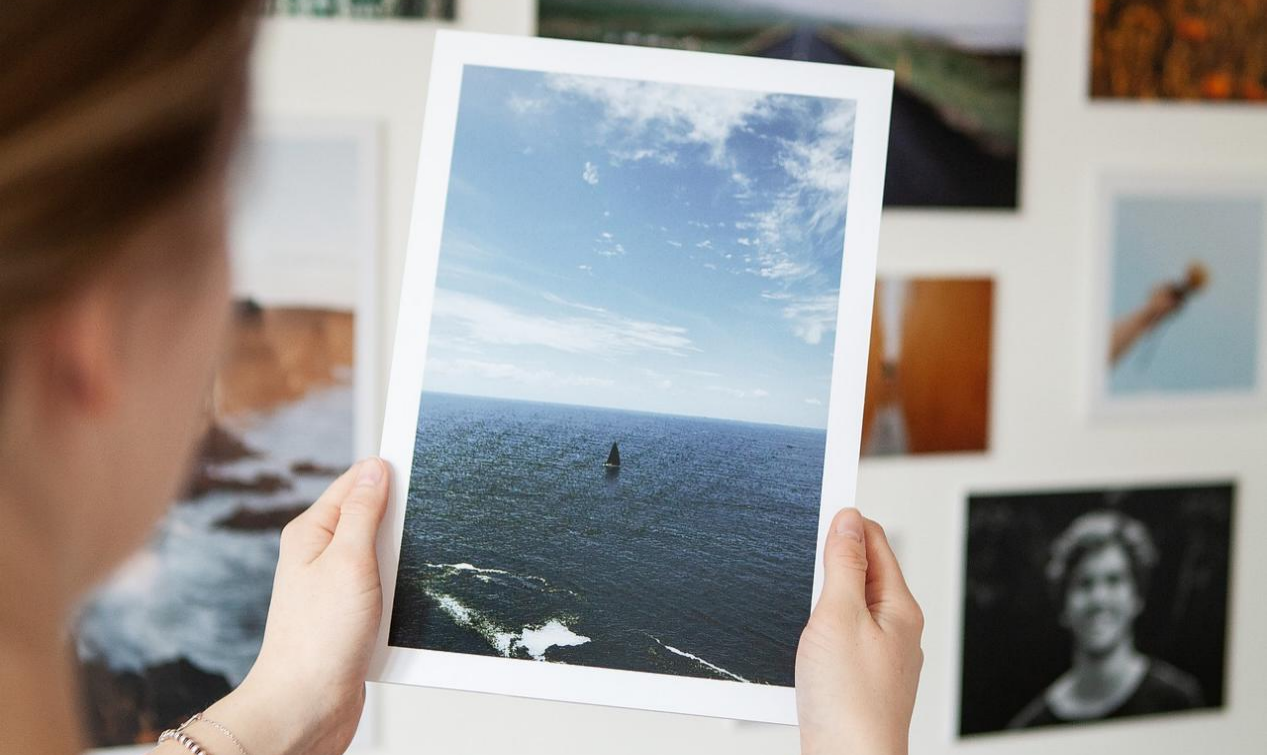
●Surface Characteristics Impact Color Rendering
Photo paper selections vary in base materials, coatings, brightness and texture - all factors influencing how inks and dyes are absorbed and colors appear. Glossy papers with polished, non-porous surfaces produce sharp details and vibrant saturation but highlight imperfections. Slightly textured luster or pearl finishes diffuse light for a softer look ideal for portraiture.
Matte papers offer the lowest contrast as their porous, fiber-based surface scatters light uniformly. While less demanding on printing precision, they reduce color gamut and can look dull compared to gloss or semi-gloss options. Heavier papers hold inks better for longevity but may show banding or graininess with lower resolution files. Thinner papers cannot hide printing deficiencies as easily.
●Match Papers to Prints for Higher Quality Rates
To leverage different papers’ properties, carefully consider image content when selecting substrates. Glossy is well-suited for landscapes with extensive gradations and sharp architectural facets. Luster flatteringly renders human skin tones while forgiving lighting issues. Metallic and specialty surfaces add dazzle suited for selective artistic use.
Print test samples to validate quality before large-scale production. Ensure color profiles accurately represent each paper’s abilities. Adjust printer settings, resolutions or post-processing as needed per substrate. Communicate paper recommendations to clients based on intended display conditions and image subject matter. With due attention paid to how specific papers shape visual qualities, photo finishing pros can optimize more prints for client delight and satisfaction.
How to Resolve Common Blistering Issues in Photo Paper?
●Analyze Main Causes
Blisters or bubbles that form pockets under the photo paper surface can damage prints and ruin clients’ images. Two primary causes include moisture trapped during printing and gaseous outgassing from paper components over time. Wet-process printing exposes paper to water, allowing humidity bubbles to become embedded. Thermal paper coatings may release gases as they cure that get pinned under layers. Improper drying, high-humidity storage or fluctuations can exacerbate existing moisture issues.
●Preventive Measures
To combat moisture accumulation, allow adequate drying time between wet-process printing steps according to paper manufacturer guidelines. Where possible, switch to alternative non-aqueous or solvent-based processes like dye sublimation that do not re-introduce water.
Carefully control heating, ventilation and humidity levels to efficiently remove moisture without introducing new pockets. Regulate temperature to avoid thermal shocks that change gas solubility under paper coatings. Store papers flat in low-moisture environments sealed from humidity fluctuations or additional moisture sources.
Inspect shipments promptly and isolate any damp or warped sheets showing signs of bubbling for separate drying before use. Pre-treat problem batches by backing them between absorbent blotters and pressing gently to wick away trapped moisture that would otherwise form bubbles over time. Implement quality controls like routine press checks to catch issues early.
By understanding photo paper composition and analyzing production variables that introduce moisture, finishing professionals gain more control over preventing and treating common blistering problems. Small preventive measures can save huge reprint costs and protect your client relationships.
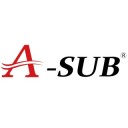