Introduction
Inkjet sticker papers have revolutionized the way we create labels, stickers and signs and are used in a wide variety of industries from commercial and industrial to personal applications. So, as a wholesaler, do you know the material composition and complex production process of inkjet sticker paper?
Inkjet sticker paper are a printable material used to create labels, stickers and signs. It consists of three main parts: face material, adhesive and liner. Facestocks can include uncoated paper, coated paper, PVC, PP or PET. Types of adhesives range from permanent to removable and repositionable, depending on the desired application. The liner acts as a backing material that protects the adhesive until the sticker is ready to use. Together, these factors determine the print quality, durability, and ease of application and removal of an inkjet self-adhesive paper.
In this article, we'll take a closer look at the material composition and production process behind inkjet sticker paper, uncovering what contributes to its exceptional quality and versatility.
Material Composition of Inkjet Sticker Paper
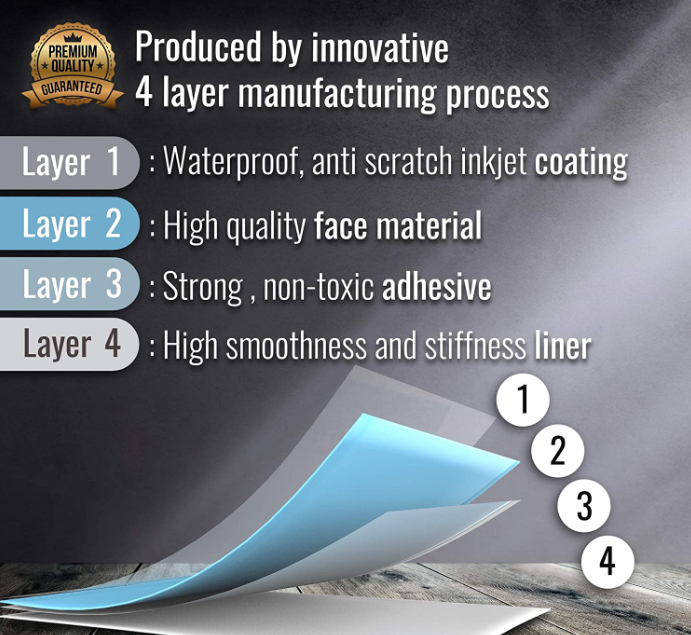
●Facestock
The facestock is the printable surface of inkjet sticker paper, and its composition plays a vital role in determining the quality and durability of the final product. There are Different types of facestock materials used in inkjet sticker paper.
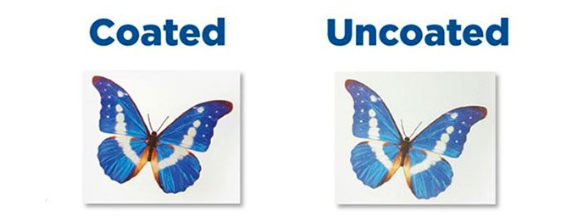
Uncoated Paper
Uncoated paper-based inkjet sticker paper provides a natural, textured finish. It is commonly used for applications that require a rustic or vintage appearance. The porous nature of uncoated paper allows for better ink absorption, resulting in vivid colors.
Coated Paper
Coated paper-based inkjet sticker paper has a smooth, glossy, or matte finish. The coating is typically made of clay or other chemicals that improve the surface smoothness and enhance print resolution. This type of sticker paper offers excellent color vibrancy and sharpness.
Polyvinyl Chloride (PVC)
PVC-based inkjet sticker paper is a synthetic material known for its durability, water resistance, and flexibility. It is widely used for applications that require long-term outdoor use or exposure to harsh environments.
Polypropylene (PP)
PP-based inkjet sticker paper is another synthetic material that combines flexibility, durability, and resistance to water and chemicals. It is often chosen for applications that require water-resistant labels or stickers.
Polyester (PET)
PET-based inkjet sticker paper is a robust synthetic material with exceptional durability and resistance to tearing, moisture, and temperature variations. It is commonly used for industrial labeling and outdoor applications.
●Adhesive
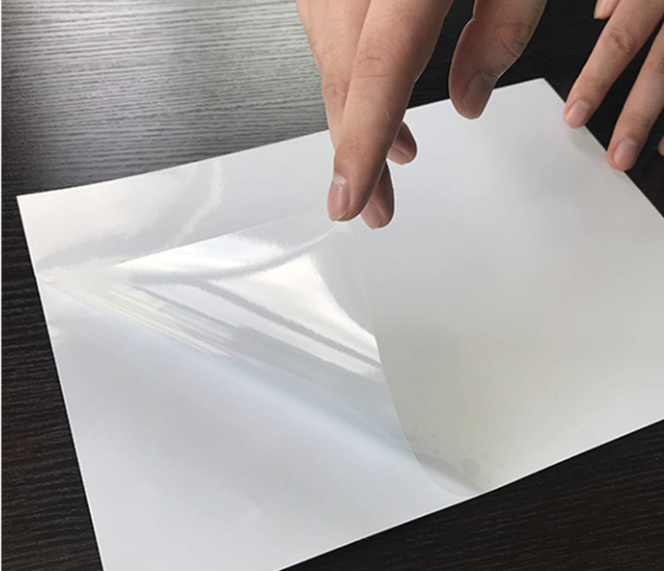
The adhesive layer on inkjet sticker paper is responsible for securely attaching the sticker to various surfaces. Different adhesive types are used based on the application requirements.
Permanent Adhesive
Permanent adhesive provides a strong bond, making it difficult to remove the sticker without residue. It is suitable for long-term applications where durability is crucial.
Removable Adhesive
Removable adhesive allows for easy removal without leaving residue or damaging the surface. It is ideal for temporary applications or situations where repositioning is necessary.
Repositionable Adhesive
Repositionable adhesive offers the flexibility to adjust and reposition the sticker during application. It provides a temporary bond that can be easily removed and reapplied multiple times.
●Liner
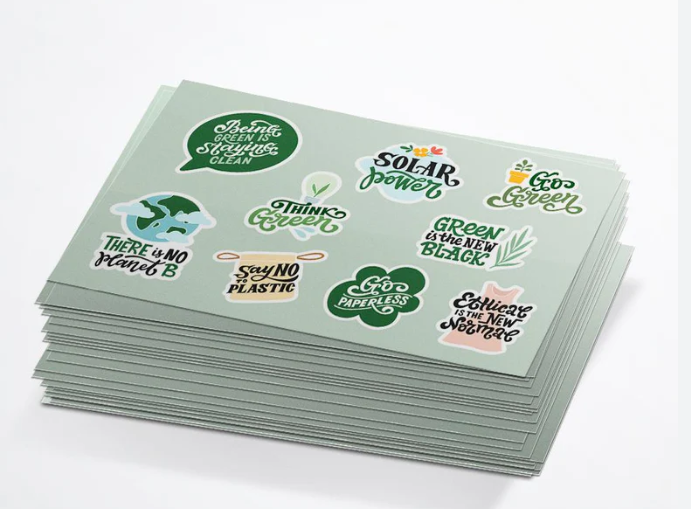
The liner is the backing material that protects the adhesive until the sticker is ready for application. Different liner materials are used based on the specific requirements.
Glassine Liner
Glassine liner is a smooth and glossy material that provides easy release of the sticker. It is commonly used for applications where the sticker needs to be peeled off quickly and efficiently.
Clay-coated Liner
Clay-coated liner offers a combination of smoothness and strength. It provides excellent stability during the printing and application processes.
Polyethylene (PE) Liner
PE liner is a flexible and moisture-resistant material. It offers good tear resistance and is suitable for applications that require added durability and protection against moisture.
A-sub inkjet self-adhesive papers are not only of high quality but also come in a wide variety, making them ideal for wholesalers. If you are interested, you can go to our official website to browse and inquire.
Production Process of Inkjet Sticker Paper
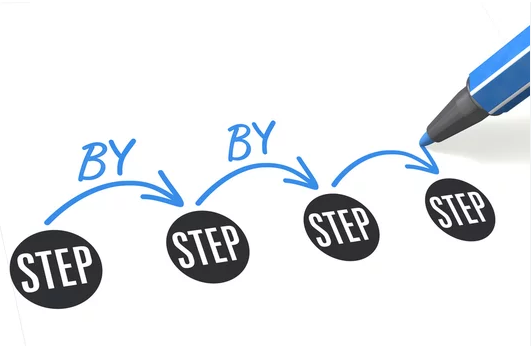
The production process of inkjet sticker paper involves several key steps.
●Substrate Preparation
For paper-based sticker paper, the paper is processed and prepared to ensure its smoothness and printability. Synthetic-based sticker paper undergoes treatment to enhance its properties, such as water and chemical resistance or flexibility.
●Coating and Lamination
In the case of paper-based sticker paper, a coating process is employed to apply a thin layer of coating material onto the substrate. This coating enhances the printability, color vibrancy, and ink absorption properties of the paper. For synthetic-based sticker paper, a lamination process is used to combine the facestock material with the adhesive layer and liner.
●Adhesive Application
The adhesive layer is applied to the facestock material using various methods such as roll coating, slot die coating, or spray coating. The choice of adhesive application method depends on factors such as adhesive type, desired adhesive thickness, and production efficiency.
●Liner Attachment
Once the adhesive is applied, the liner material is attached to the adhesive layer to protect it until the sticker is ready for use. The liner attachment process involves precise alignment and bonding techniques to ensure proper release properties and ease of application.
Tips for Choosing and Using Inkjet Sticker Paper
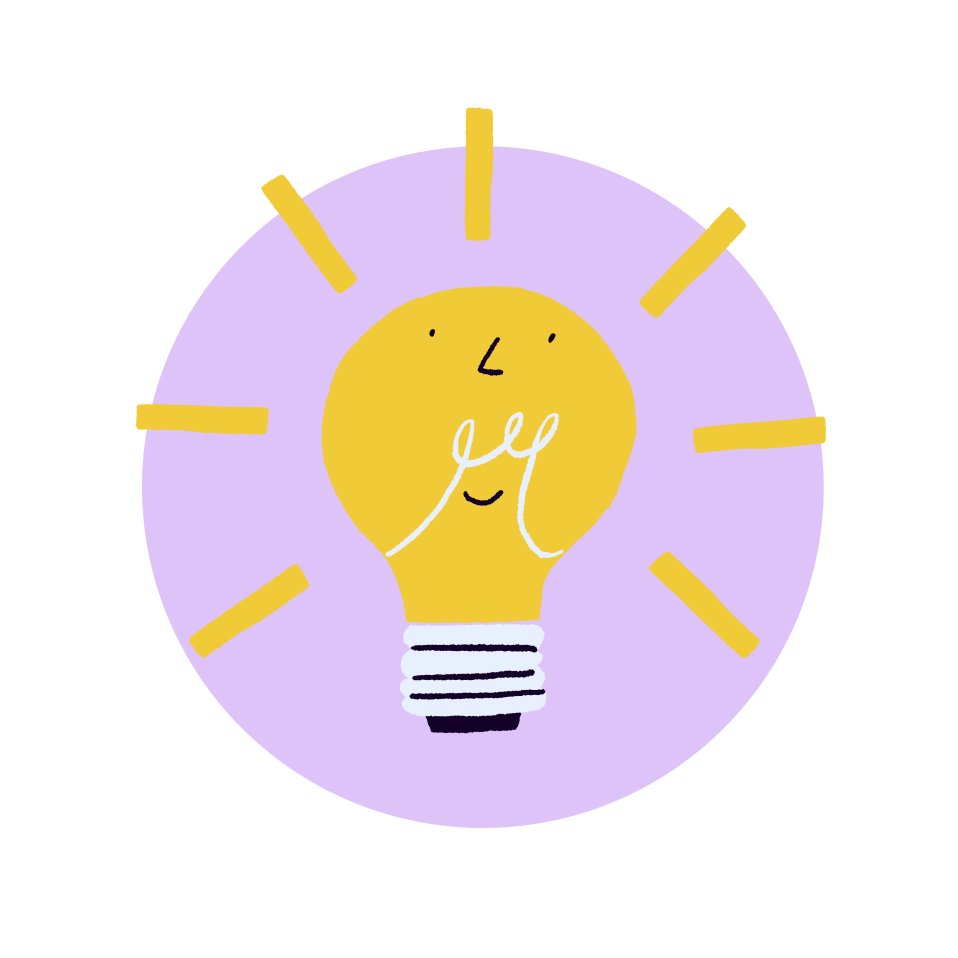
●Consider the application requirements
Determine whether a permanent, removable, or repositionable adhesive is needed based on the intended use and surface type.
●Select the appropriate facestock material
Consider factors such as desired finish (glossy, matte, or textured), durability requirements, and compatibility with the printing technology used.
●Evaluate liner properties
Choose a liner material that offers easy release properties and stability during the printing and application processes.
●Test print compatibility
Before bulk printing, perform a test print to ensure compatibility between the inkjet printer and the inkjet sticker paper. This helps avoid potential issues such as ink smudging or poor print quality.
●Follow proper storage and handling guidelines
Store inkjet sticker paper in a cool, dry environment to maintain its quality. Avoid exposing it to extreme temperatures or high humidity levels.
●Surface preparation
Ensure that the surface where the sticker will be applied is clean, dry, and free from any dust, oils, or debris. This helps to achieve better adhesive bonding and longevity.
Conclusion
Inkjet sticker paper is a versatile material that finds extensive applications in various industries. Understanding its material composition and production process is essential for selecting the right type of inkjet sticker paper for specific applications. By considering factors such as facestock material, adhesive type, and liner properties, users can ensure optimal print quality, durability, and ease of application. With the right inkjet sticker paper, businesses and individuals can unleash their creativity and effectively communicate their messages through vibrant and visually appealing stickers and labels.
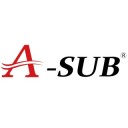