Intro
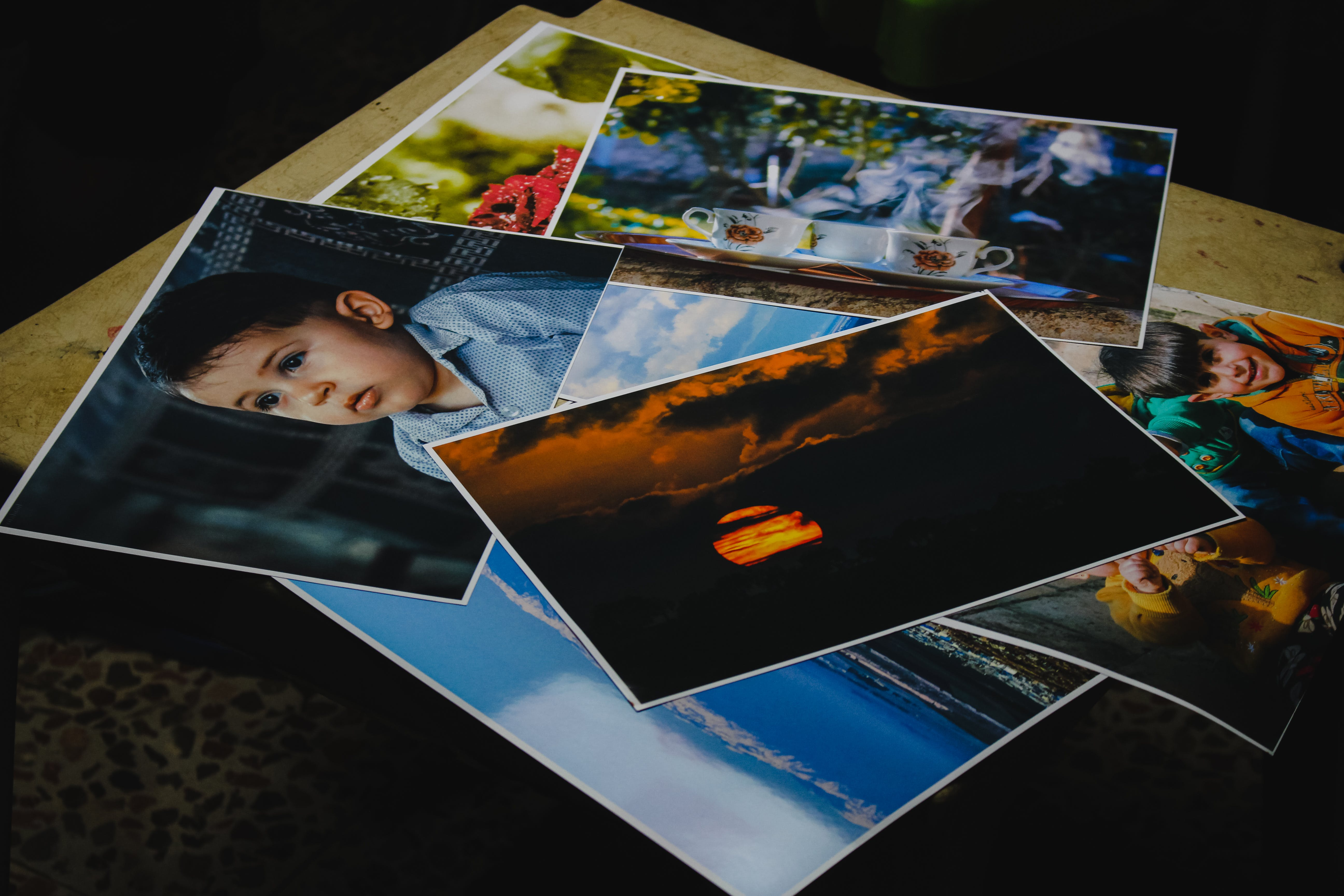
●Define Custom Photo Paper and its Importance
Custom photo paper refers to photo printable media that can be tailored to meet specific customer needs and applications. Compared to regular stock photo papers available in standardized sizes and finishes, custom photo paper offers more flexibility in specifications such as paper thickness, surface texture, dimensions, and other properties. This allows customers to have photo prints or materials designed precisely for their intended purpose.
Producing photo prints or materials according to custom technical specifications has become increasingly important in various industries and use cases. For professional photographers, custom paper choice and sizing are crucial for exhibition printing and high-quality portfolio presentation. Brands and exhibitors also rely on custom photo papers for commercial displays at events, instore promotions, and outdoor advertising. Other common applications include specialized photo products for commemorative occasions, artistic pieces, self-publishing projects, and customized gift wraps or stationery.
●Purpose of this Article is to Discuss the 3 Essentials
Despite the growing demand, creating quality custom photo papers with consistency poses unique challenges. This article aims to outline the three essential factors that wholesalers and printers must master in order to deliver premium custom products that satisfy clients. Specifically, it will examine the importance of careful material selection, design detailing, and production quality control. Understanding these basics can help both clients and vendors ensure optimal results for their custom photo paper projects. With the right expertise in these three pillars, one can open up new possibilities through targeted custom solutions.
In the following sections, each essential will be discussed in detail through practical examples and best practices. Readers will learn how these elements tie into the complete customization workflow from planning to fulfillment. It is our goal to equip readers with fundamental knowledge for fruitful partnerships in the custom photo paper field.
Essential 1: Material Selection
●Explain Different Types of Photo Paper Materials
There is a wide variety of photo paper materials available for custom projects. The most common types are resin-coated paper, fiber-based paper, and synthetic paper. Resin-coated paper features a layer of polyethylene on a paper base for excellent moisture resistance and durability. It produces sharp images and is ideal for high-quality prints. Fiber-based papers like cotton are soft and produce natural colors but are less water-resistant. Synthetic papers are made of polyester materials and offer weatherproof and tear-resistant properties well-suited for outdoor displays.
There is a wide variety of photo paper materials available for custom projects. The most common types are resin-coated paper, fiber-based paper, and synthetic paper. Resin-coated paper features a layer of polyethylene on a paper base for excellent moisture resistance and durability. It produces sharp images and is ideal for high-quality prints. Fiber-based papers like cotton are soft and produce natural colors but are less water-resistant. Synthetic papers are made of polyester materials and offer weatherproof and tear-resistant properties well-suited for outdoor displays.
●How to Select the Suitable Material Based on Project Needs
Proper material selection is key to meeting client requirements. Aspects to consider include intended use, budget, expected lifespan, display conditions, and finishing needs. For example, resin papers suit galleries but may be expensive for large volume orders. Tyvek would survive protests but lack aesthetic qualities for portraits. Communication with clients is important to understand specifications and balance priorities. Samples can help clients visualize options before deciding. Wholesalers should recommend alternatives factoring technical capability and also suggest value-added services like lamination.
●Material Affects Quality, Applications, Price etc.
The right paper choice greatly impacts end results. More durable materials uphold image quality longer during use. Acid-free or archival papers prevent discoloration. Textures influence viewing experience. Waterproofing protects prints for wet areas. Heavier paper weights lend prestige. Price usually rises with specialized characteristics and non-standard sizes. Overall, material is a foundation for quality custom outputs and stays within budget goals. Its importance cannot be understated.
Essential 2: Design Details
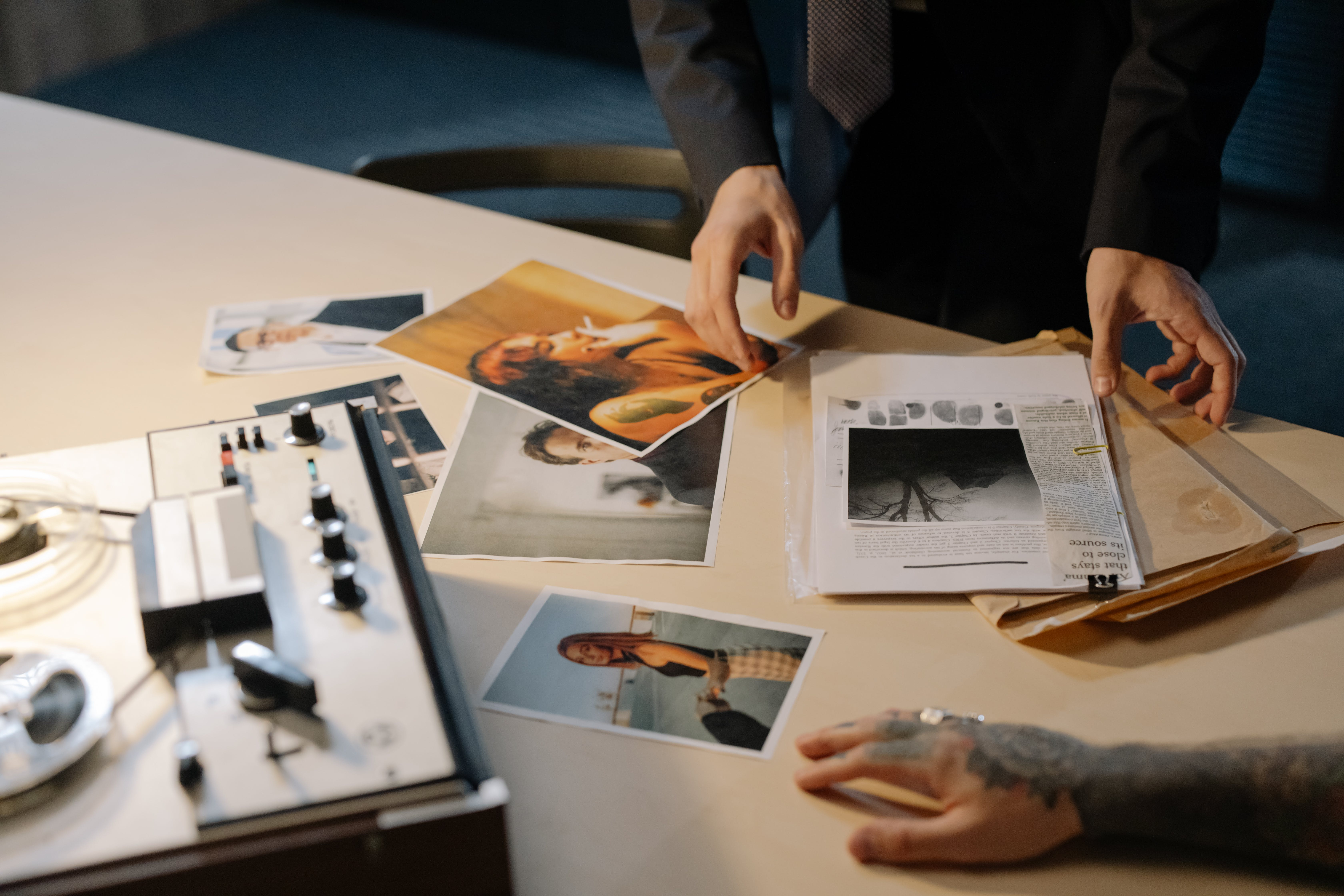
●Graphic Design is Key to Custom Print Quality
For custom prints, the graphic design stage heavily impacts the final product appearance and reception. As no two designs are alike, precise control over design elements becomes critical. A single pixel misaligned or color cast can ruin an otherwise flawless piece. Those producing custom designs must have solid expertise in areas like layout, typography, image preparation and color management.
●Discuss Elements like Image, Layout, Color Matching
Images must be high resolution without pixilation, especially for enlargement. Effective layout ensures focal points stand out and complement the intended viewing environment, whether close-up desk frames or long-distance billboards. Readability of text-based designs relies on legible font choice and size. Color accuracy from design to printoutput hinges on calibrating monitors to industry profiles like SWOP. Even minor mismatches in hue or tone can mar perceived quality. It also requires considering substrate color effects like how images manifest on white versus transparent papers.
●Examples of Good and Bad Design Practices
Good designs provide visual hierarchy through repetition, proportion and spacing principles. Cluttered compositions diminish impact versus spaced-out designs allowing focus. Consistent styling maintains cohesion across a product series. Technical preparations like rasterizing vector elements and flattening layers aid print production. Bad habits are improperly sized or mismatched elements, illegible serif fonts for large-scale viewing, unoptimized files bloating file sizes, and uncalibrated soft-proofs deceiving the real printed result. Attention to details at every stage avoids pitfalls and realizes the designer’s vision perfectly on paper. It is an art as much as science for satisfying custom output.
Essential 3: Production Technology
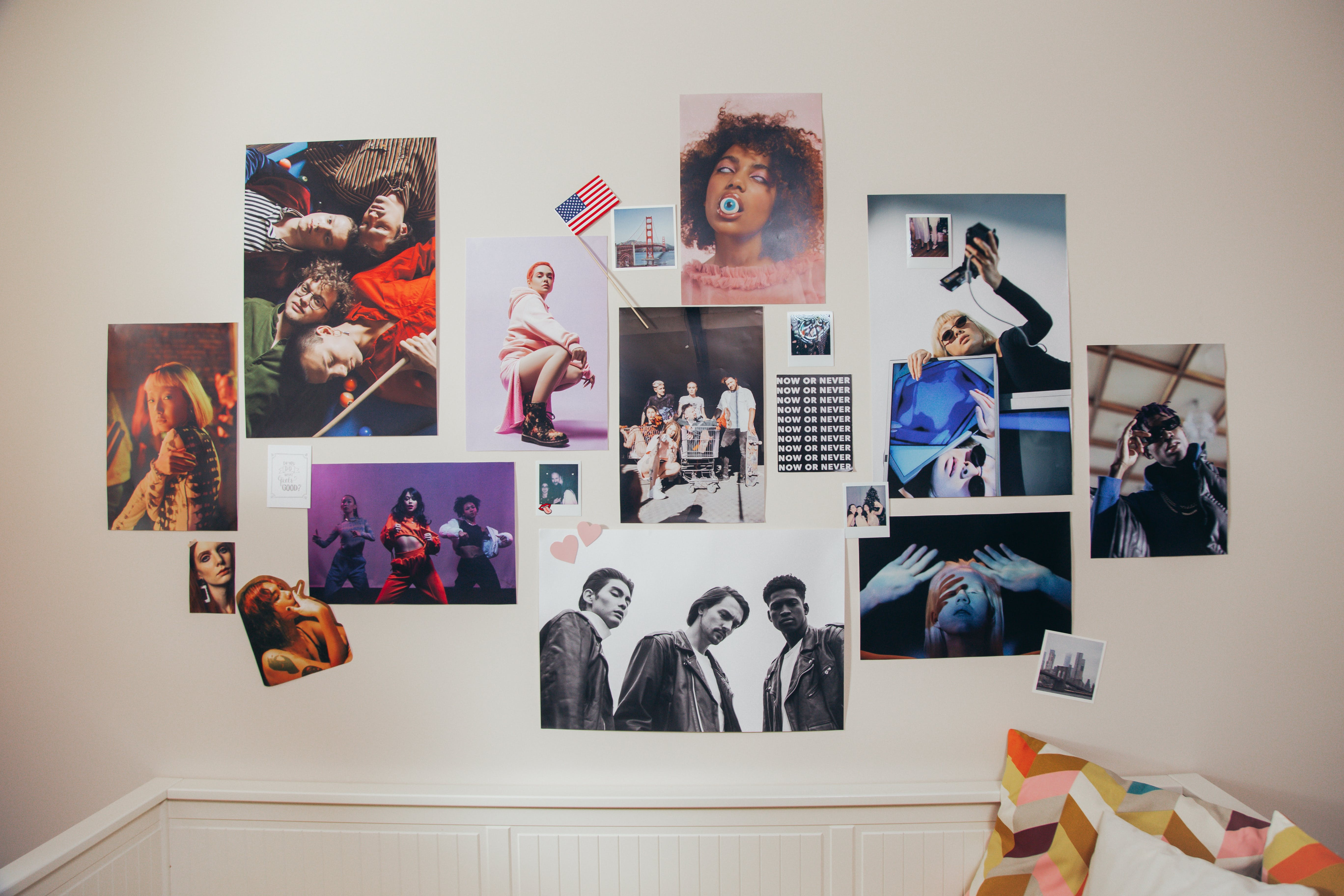
●Digital printing and Sublimation Process
Common production methods for custom papers include inkjet printing and dye sublimation. Inkjet employs pigment or dye-based inks deposited via printheads onto substrates. Sublimation utilizes heat to transfer dye from a solid form to a gas then absorbed into the substrate's fibers in vibrant permanence. Both require calibrated machines and controlled environments for consistency. Operators must be specially trained to handle technical process variables precisely.
●Emphasis on Process Control and Quality Standards
Quality assurance is paramount as even minor deviations cause defects. Standard operating procedures ensure uniform settings over time and across multiple operators and shifts. Calibrations with specialized tools optimize droplet size and density. Careful monitoring of factors like temperature, pressure, and drying prevents medium or long-term defects. Automation aids maintaining tight specifications. Routine audits check for process drift and improvements.
●Ensuring Consistency across Mass Production
For bulk custom orders, maintaining quality at high-volumes poses unique challenges. Samples are crucial to establish baselines before larger runs. Inline inspection identifies issues promptly. Statistical process controls featuring sampling check conformity and also catch assignable and common causes of variation for prevention. Consistency in materials handling, packaging and shipping protects the finished products. Adhering to rigorous manufacturing protocol delivers an outstanding product experience for clients, no matter the order size.Conclusion
●Recap the 3 Essential Factors
In summary, the key pillars for high-quality custom photo paper outputs are material selection, design detailing, and production proficiency. Meeting client specifications requires expertise across each domain as they work synergistically towards the end goal. An optimum formula combines suitable substrate choices, well-executed graphic designs, and consistency in digital or thermal processes no matter the order size. When these essentials are properly addressed, custom labs enable hitherto limited applications through carefully crafted solutions.
●Provide Tips to Work with Custom Lab
When partnering with custom suppliers, clearly communicate requirements and solicit recommendations upfront. Ask about certification, industry experience, previous similar projects for confidence. Discuss turnaround expectations realistically considering order complexities. Request samples before sign-off. Provide high quality ready-to-print design files according to supplier guidelines. Maintain open collaboration throughout changes or reworks.
●Customer Service also Plays an Important Role
Beyond technical prowess, superior customer experience stems from approachability, quick response times, order tracking visibility and proactive issue resolution. Competent customer support aids smooth projects from briefing to delivery. Post-production care like usage guides and lifetime technical assistance maintains relationships. Client satisfaction drives positive word-of-mouth and repeat custom orders. Overall, marrying professional capabilities with a customer-centric attitude consistently delivers customer delight.
In conclusion, internalizing these three essentials fosters fruitful partnerships between clients and suppliers within the burgeoning custom photo paper field. With continued cooperation, limitless possibilities can be realized.
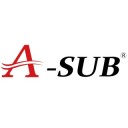