Intro
●Why Inventory Management Matters for Photo Paper Bulk
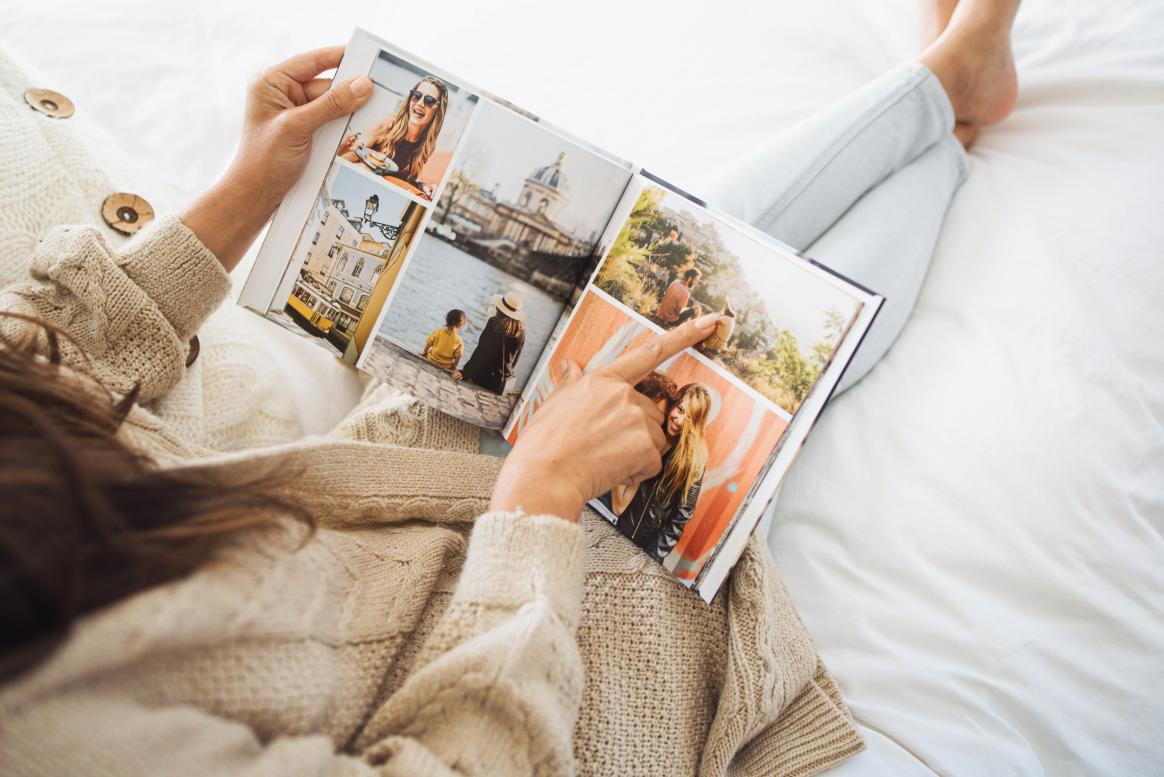
For any retailer, lab, or printing business that purchases photo paper in bulk quantities, effective inventory management is crucial. Photo paper has a limited shelf life, typically just 6-12 months from the manufacture date before print quality may begin deteriorating. Since bulk orders often consist of thousands of sheets of different paper types, sizes, and brands, there is significant money tied up in storage. Overstocks can quickly go to waste if not tracked carefully. Meanwhile, stockouts are detrimental, disrupting workflows and injuring customer satisfaction. Tight inventory controls are therefore needed to avoid excess holding costs while maintaining adequate stocks to serve client needs.
Proper management is also important from a sustainability perspective. As an environmental leader, the photo industry is continuously seeking ways to reduce paper usage and minimize waste at all stages of the supply chain. By ensuring bulk paper inventory is rotated on a first-in-first-out basis and that reorder points are calibrated to true needs, businesses can better avoid outdated product ends up being discarded. Conserving resources in this way has economic benefits as well helps photo companies lessen their carbon footprint.
●Goals of Managing Photo Paper Bulk Stock Effectively
The primary objectives of implementing robust inventory processes for bulk photo paper supplies are four-fold. First, optimal management aims to keep inventory carrying costs as low as possible by limiting stock levels of inactive items or those nearing expiration. Secondly, it helps avoid stockouts and backorders that negatively impact customer service. Thirdly, effective management can reduce paper spoilage and waste from goods expiring in storage. Finally, the goal is to provide real-time visibility into stock on hand so reorders are placed precisely when needed, neither too early nor too late. Achieving these aims through diligent inventory tracking and controls leads to significant cost savings as well higher productivity and customer retention rates over the long run.
Planning Bulk Photo Paper Purchases
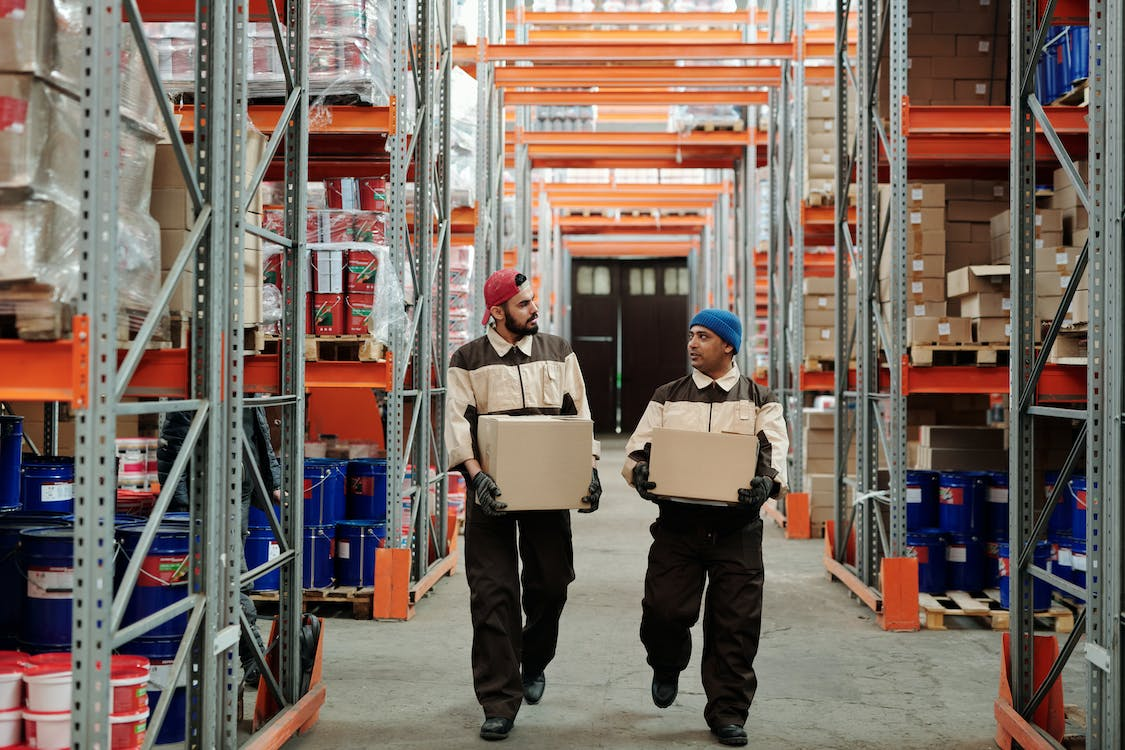
●Determining Your Store/lab’s Monthly Printing Needs
The first step in purchasing bulk photo paper is analyzing historic sales data to calculate the average quantity of each paper type and size sold per month. Factors like print volume, mix of retail versus commercial orders, and new product offerings will impact needs. Be sure to also account for planned changes that may alter demand. Maintaining rolling 12-month data allows for monthly usage comparisons to spot trends.
●Forecasting Seasonal Demand Variations
Understanding seasonality is also important when budgeting for paper requirements. For example, demand often peaks around major holidays. Other factors like back-to-school rushes, seasonal retail promotions, or local events must also be incorporated into projections. Estimating monthly fluctuations prevent both under-stocking during high-use periods as well as over-purchasing when volume is typically lower.
●Considering Lead Times When Reordering
Lead times for bulk photo paper orders are typically several weeks. Thus, the reorder point should be set multiple weeks in advance of a store’s projected use date to allow sufficient time for replenishment. Checking with suppliers on their standard and rush delivery schedules aids this planning process. Building in appropriate lead times helps minimize stockouts.
●Purchasing Appropriate Bulk Quantities
Once monthly needs are forecast and lead times accounted for, bulk order quantities can be determined. Industry norms usually recommend maintaining 1-2 months of stock, though this may vary depending on factors like storage space restrictions or supplier MOQs. Placing larger periodic orders rather than small frequent ones can also garner volume discounts to offset increased capital tied up in inventory.
Setting Up Your Storage
●Designating A Storage Space
Allocating a reserved, dry, cool space for photo paper bulk storage is important. The location should be away from direct sunlight, heat sources, and areas prone to moisture/humidity fluctuations. Measure shelving/stocking needs based on the largest storage capacity anticipated. Proper ventilation is also required.
●Organizing by Paper Type/size/brand
Sorting inventory systematically makes auditing, counting and distributing easier. Group items together based on relevant attributes like paper surface, size or manufacturer. Label aisles/shelves clearly so products are easy to locate. Rotate stock using plastic bins, boxes or wrappings labeled with contents.
●Using Shelves, Pallets, Bins Appropriately
Effectively utilizing shelves, pallets and stackable containers maximizes available space. Heavier items like boxes full of 8x10 paper or larger should be stored closer to the ground and consolidated on pallets when possible. Lighter paper packs or smaller sizes can be arrayed higher up. Bins help organize mixed SKUs.
●Arranging for First-in, First-out Handling
To abide FIFO principles, new shipments should be placed behind existing stock so older inventory is depleted first. Date all incoming bulk paper shipments upon receipt and storage. Doing so allows you to clearly see what was placed in storage first to avoid accidentally selecting more recently delivered goods first when replenishing inventory. These practices extend the viable shelf life of photo paper supplies.
Tracking Your Inventory
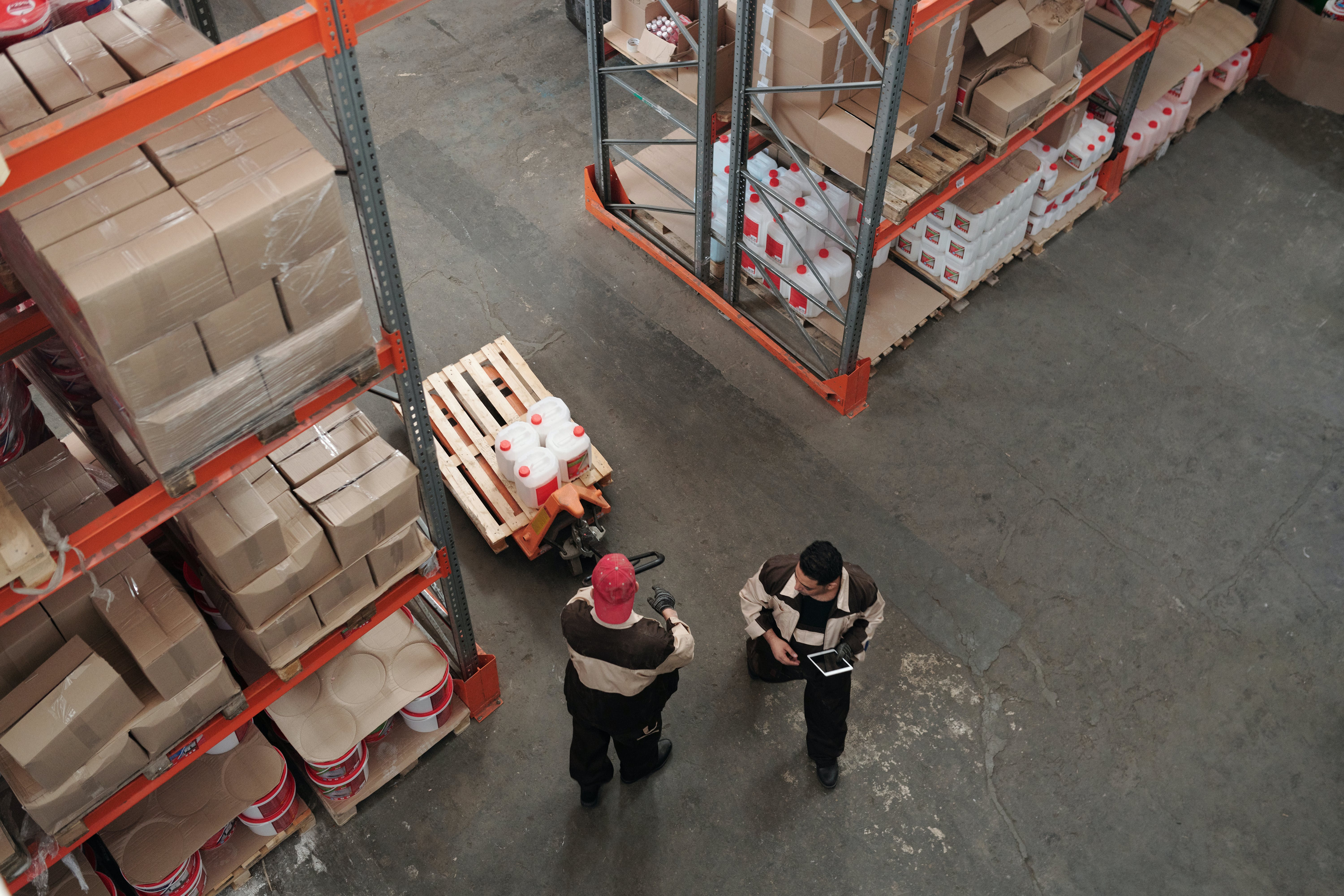
●Choosing Inventory Management Software
Leverage technology to simplify paper tracking with software tailored for businesses. Key features include barcode scanning, mobile access, automated reorders, usage tracking and reporting. Integrations with accounting software automate finances.
Consider solutions sized for company needs from free/open-source to robust paid programs.
●Setting Par Levels for Reordering
Set minimum (par) and maximum (like 1-2 months’ stock) inventory levels for automatically generating replenishment orders. Levels should factor time to delivery and usage rate variability. Test conservative settings initially, making adjustments after a few reorder cycles.
●Conducting Regular Cycle Counts
Counts keep records accurate, catching discrepancies early. Schedule them monthly, particularly after busy seasons. Conduct full physical inventories of storage biannually and sample counts of fast-movers quarterly. Print reports for review, noting overages/shortages. Update to reflect real quantities and order status changes.
●Recording Usage Data Over Time
Document paper quantities with each order shipment, sale or project. Note sizes, surface and quantity. Periodically analyze type/volume trends, changing order patterns or seasonal fluctuations to recalibrate forecasts and storage allocation. Flag usage increases/decreases by 10% for follow up. Create seasonal adjustment factors as needed.
Routinely tracking supply stock levels, movements and consumption through technology and warehouse audits creates visibility into what’s needed, when. It ensures the right paper amounts are always available while avoiding overstocking.
Improving Inventory Forecasts
●Analyzing Past Order Patterns
Evaluate order histories to determine the most common paper types, formats and quantities purchased each month. Note any trends, such as increased softcover book printing in fall. Forecasts should be based on multiple years of historical data if available to accommodate fluctuations.
●Factoring in New Product Lines/services
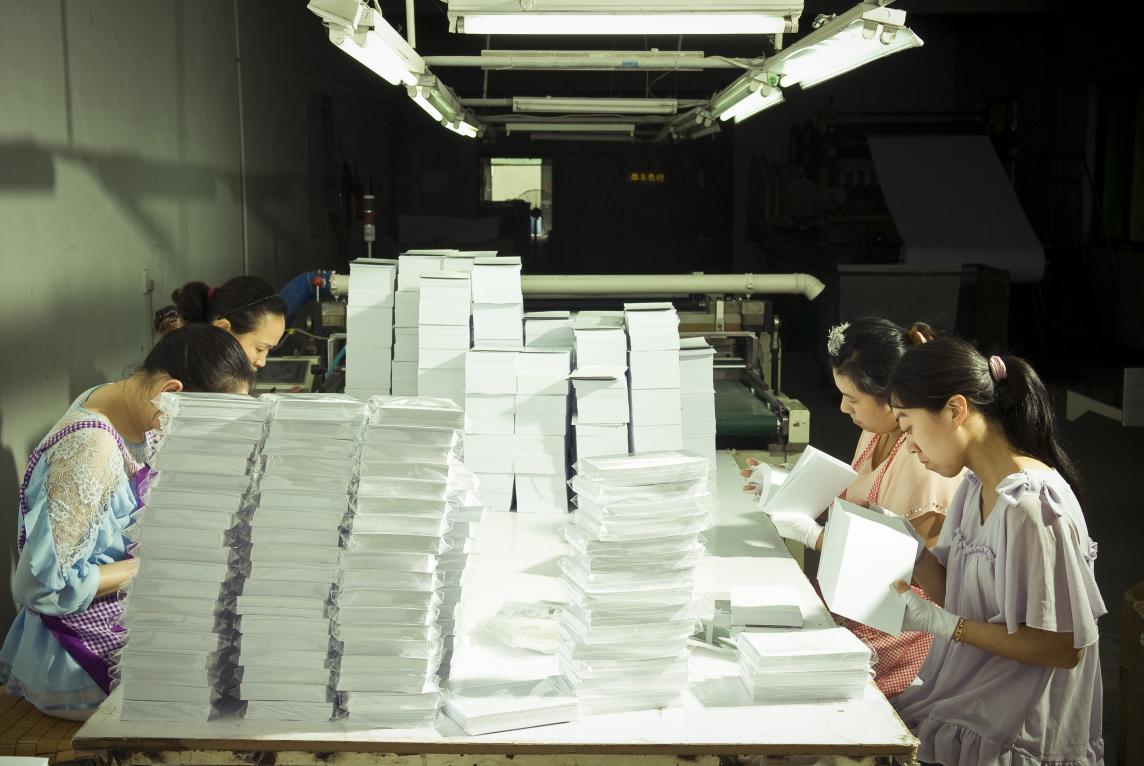
Consider adding new offerings to lines when projecting needs. For example, adding passport photo services likely increases 4x6 paper demand. Upgrading lab equipment may change substrate preferences. Test market-test new products to estimate impacts on ordering patterns.
●Adjusting for Changes in Sales/operations
Recognize that strategies, team structures and market forces evolve. Compare prior year sales by quarter to identify slipping or outpacing categories for modifications. Note new account wins, losses or production shifts that deviate from the norm. Incorporate anticipated closed locations, renovations or holidays into planning.
●Updating Forecasts Quarterly
Set aside time each quarter to refine models using year-over-year monthly sales, current inventory levels and adjusted quadrants. Factor latest sales promotions, seasonal trends, vendor lead times and unpredicted irregularities identified. Document rationale and obtain sign off for forthcoming financial planning. Finetune assumptions as real data emerges.
Frequent forecasting reviews coupled with exploring all external influences provide the most accurate projections for bulk ordering. This ensures stock stays lean while steadfastly serving printing needs.
Minimizing Waste and Spoilage
●Checking Expiration Dates upon Receipt
Photo paper generally expires 6-12 months after manufacture. Note shipment dates and do shelf life calculations to identify earliest and latest expirations. Strategically store inventory together based on expiration with closest-dated in front.
●Rotating Stock Using FIFO Practices
Always pull oldest stock first to consume within expiration period. Date all shipments received and periodically audit storage to confirm the procedure, adjusting as needed. First expired/first out (FEFO) further extends usability.
●Ordering Sufficient Quantities
Oversupply depletes cash flow and leads to avoidable waste when stock expires on the shelf. Conversely, low safety levels increase stockout risks. Maintain recommended cover of 1-2 months based on forecasts, ensuring all paper moves in time.
●Donating/returning Unused Surplus
Despite best efforts, some excess may remain as expiration nears. Request credit from vendors for return, or donate unopened paper to charitable photo programs and schools. This recoups value and prevents landfill disposed paper that would otherwise become obsolete.
Regularly auditing dates, frequent rotation and maintaining prudent order amounts helps optimize the usage lifecycle of each bulk paper shipment to minimize reductions to operating margins andincrease sustainability.
Reviewing Inventory Metrics
●Days of Supply on Hand
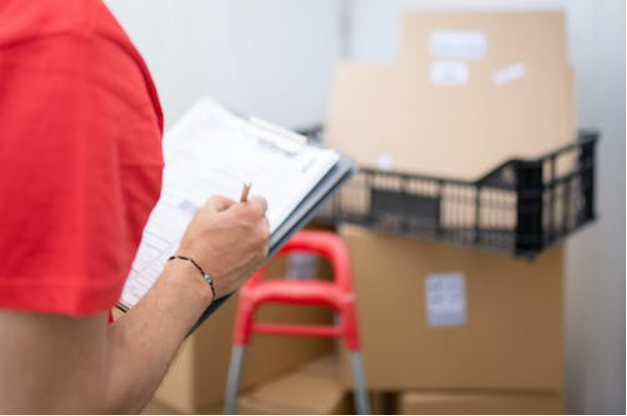
Calculated as quantity on shelf divided by daily usage rate, this indicates time inventory will last if no additional orders are placed. Industry averages 60-90 days while too high ties up capital and increases waste risk.
●Stockouts and Overstocks
Note frequency and value of stockouts or held inventory that reaches expiration without selling, using annual dollar cost averaging. High figures signal forecasting issues requiring adjustment.
●Inventory Turnover Rate
Derived from cost of goods sold divided by average inventory value, this compares annual sales to stock levels. Higher is preferable, aiming 4-6 turns which means full inventory sells 1-2 times per year.
●Dollar and Quantity Variances
Review value and unit discrepancies between inventory counts and system records monthly. Identify possible causes like data entry errors or cycle counting flaws. Resolve variances over tolerance levels.
Quarterly report comparisons to key performance indicators (KPI) like above help assess progress of inventory management program improvements. It also reveals developing issues regarding specific paper types or suppliers for swift remedy. Metrics provide an objective understanding of stocking decisions to enhance profitability over time.
Further Optimization Strategies
●Cross-docking between Locations
For businesses with multiple sites, cross-docking involves directly shipping orders between stores rather than warehousing, reducing stock levels. Ensure inter-location paper transfers occur based on par levels and fulfillment timelines are mutually agreed.
●Just-in-time Inventory Techniques
JIT aims to receive inventory only as products are needed to manufacture/ship orders. For photo paper, this entails placing replenishment orders upon reaching minimum levels so that the most up-to-date paper is consistently available. Collaborate closely with trusted suppliers.
●Vendor-managed Inventory Programs
Some large-volume buyers implement VMI where suppliers retain ownership of certain paper types kept on-site. The vendor monitors stock levels, initiates replenishments, and bears inventory risk according to prearranged algorithms. This streamlines procurement.
●Consignment Options for Large Buyers
Photo manufacturers may store bulk goods at client locations essentially on loan, invoicing only when paper is consumed. This eliminates up-front payment commitment and capital expenditure for strategic customers capable of maintaining agreed safety levels through web portal views.
Implementing approaches like these refine traditional inventory models and further optimize processes, cost control and space utilization for high functioning print operations once fundamentals are established. Ongoing evaluation of new strategies enhances competitive edge.
Conclusion
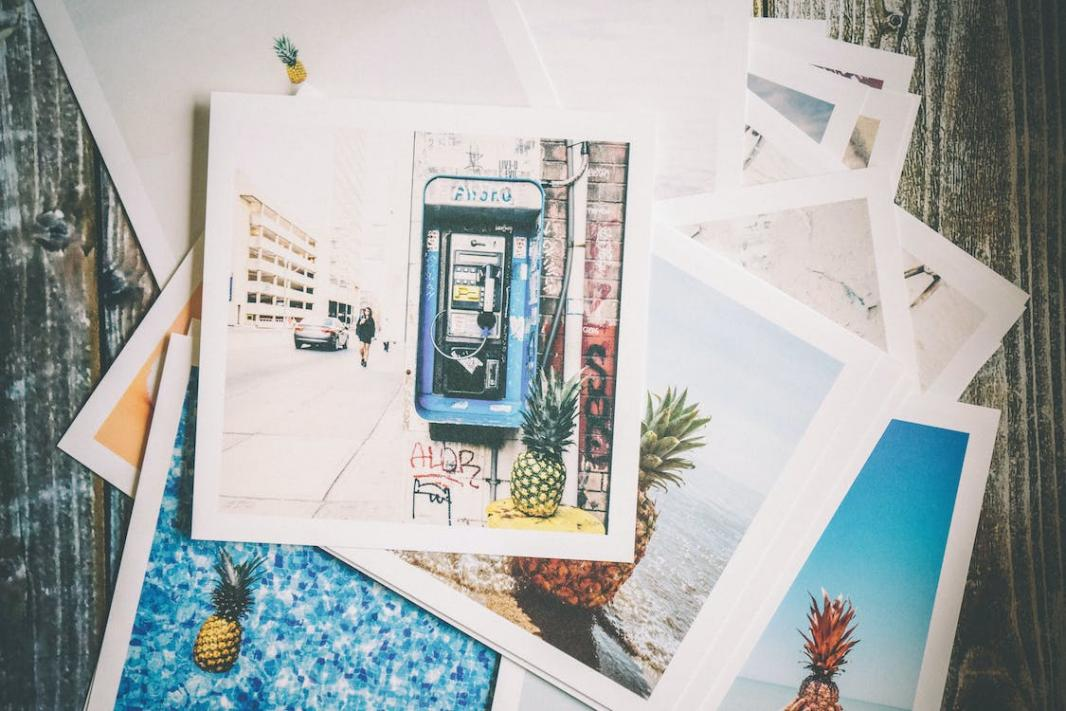
Effective management of bulk photo paper inventory is critical for photography
retailers and printing businesses. It helps ensure an adequate, high-quality paper supply while minimizing waste and reducing operational costs. With photo paper having a limited shelf life and constituting a major expense, tight inventory controls are necessary.
This article provided numerous tips and best practices for planning purchases, setting up storage, tracking stock, improving forecasts, reducing spoilage, reviewing metrics, and employing advanced strategies. By determining monthly needs, accounting for seasonality, maintaining proper stocking levels, and constantly refining processes, companies can keep inventory carrying costs low and avoid stockouts.
Regular cycle counts, analyzing consumption data, and adjusting reorder points prevent expiration of bulk supplies in storage. Techniques like first expiry first out, periodic forecast reviews, and cross-docking between locations also maximize paper usage. For larger buyers, vendor-managed programs and consignment options offer enhanced efficiency.
Overall, a laser focus on inventory management delivers substantial financial benefits and boosts customer satisfaction. Photo retailers that implement the fundamental recommendations discussed will streamline their bulk paper supply chains and operations for greater profitability and sustainability long into the future. Effective stock controls and replenishment procedures are key to business success.
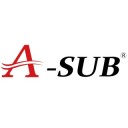