Intro
Labels play a vital role in branding, product identification, and information dissemination.They are more than just stickers. They are powerful marketing tools that represent your brand and help differentiate your products from competitors. Well-designed labels attract attention, build trust, and leave a positive impression on consumers. They convey important information such as product names, ingredients, and usage instructions, influencing purchasing decisions. So, Choosing the right label manufacturer for your business is crucial.
This article highlights the importance of selecting a suitable label manufacturer by discussing key considerations such as experience, production capabilities, quality control measures, customer support, and pricing. It provides valuable insights for making an informed decision in choosing the right partner for label production.
Experience and Expertise
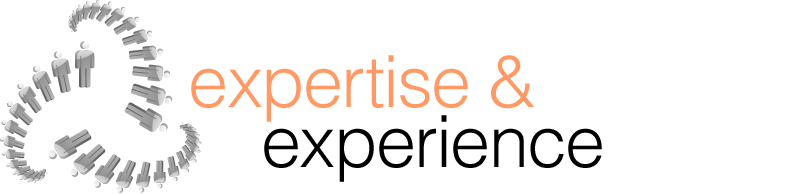
When considering a label manufacturer, it is important to assess their experience and expertise in the industry. Here are some questions to ask:
●How long has the label manufacturer been in business?
The longevity of a label manufacturer's operation can indicate their stability and industry knowledge. A manufacturer with years of experience is more likely to have refined their processes and developed a deep understanding of label production.
●Do they specialize in specific types of labels or offer a wide range of options?
Some label manufacturers specialize in specific types of labels, such as food packaging labels, pharmaceutical labels, or industrial labels. Determine if their specialization aligns with your needs. Alternatively, you may prefer a manufacturer that offers a wide range of label options to accommodate different products or applications.
●Can they provide case studies or examples of their previous work?
Reviewing case studies or examples of a label manufacturer's previous work can give you insights into their capabilities and quality. Ask for samples they have produced for other clients. This will help you assess their ability to meet requirements.
By evaluating a label manufacturer's experience and expertise, you can make an informed decision about their suitability for your label production needs. Remember to align their experience with your industry, assess their specialization, and request examples of their previous work to ensure they meet your expectations.
Production Capabilities
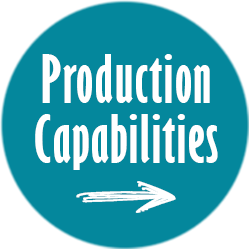
When assessing a label manufacturer, it is important to understand their production capabilities. Here are some key questions to ask:
●Can they accommodate different label sizes, shapes, and materials?
Check if the label manufacturer can accommodate your specific requirements in terms of label sizes, shapes, and materials. Labels come in various dimensions and can be die-cut into custom shapes. Additionally, labels can be printed on different materials like paper, vinyl, or film. Ensure the manufacturer has the flexibility to fulfill your unique needs.
●Do they offer customization options, such as foiling, embossing, or specialized finishes?
If you desire specialized finishes or customization options for your labels, inquire whether the manufacturer provides these services. Options like foiling, embossing, spot varnishing, or textured finishes can enhance the visual appeal and tactile experience of your labels. Determine if the manufacturer can accommodate these customizations.
●What is their production capacity and turnaround time?
Understanding the label manufacturer's production capacity and turnaround time is crucial for planning your labeling needs. Inquire about their production capacity to ensure they can handle your order volume efficiently. Additionally, ask about their typical turnaround time from order placement to label delivery. This information will help you manage your timelines and meet your business requirements.
By assessing a label manufacturer's production capabilities, you can ensure they have the technological capabilities to meet your label specifications. Consider their printing technologies, ability to accommodate different sizes and materials, availability of customization options, and their production capacity and turnaround time to make an informed decision about partnering with them.
Quality Control
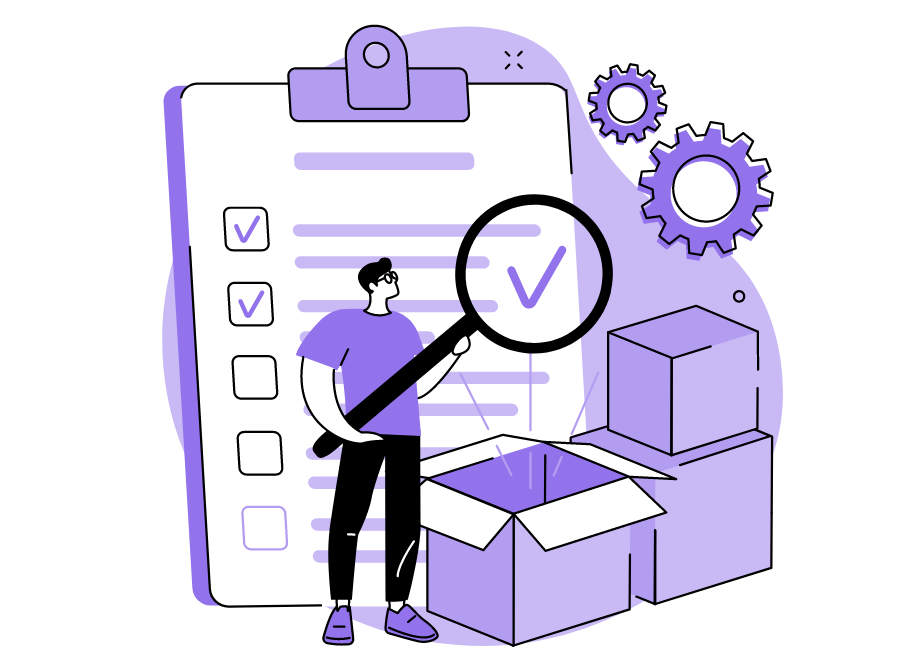
Ensuring the quality of your labels is paramount. When evaluating a label manufacturer, consider the following questions regarding their quality control measures:
●What quality control measures do they have in place during the manufacturing process?
Inquire about the label manufacturer's quality control procedures. Ask about the steps they take to ensure that each label meets the required standards. This may include inspections at various stages of the manufacturing process, quality checks for alignment and verification of adhesive strength.
●Can they provide samples or references from satisfied customers?
Request samples of labels they have produced in the past to assess the quality of their work. Examining actual labels will allow you to evaluate print clarity, color vibrancy, and overall craftsmanship. Additionally, ask for references from satisfied customers who can provide insights into their experience working with the manufacturer.
By asking these questions about quality control, and samples, you can gain assurance that the label manufacturer prioritizes quality and is committed to delivering labels that meet your expectations.
Customer Support
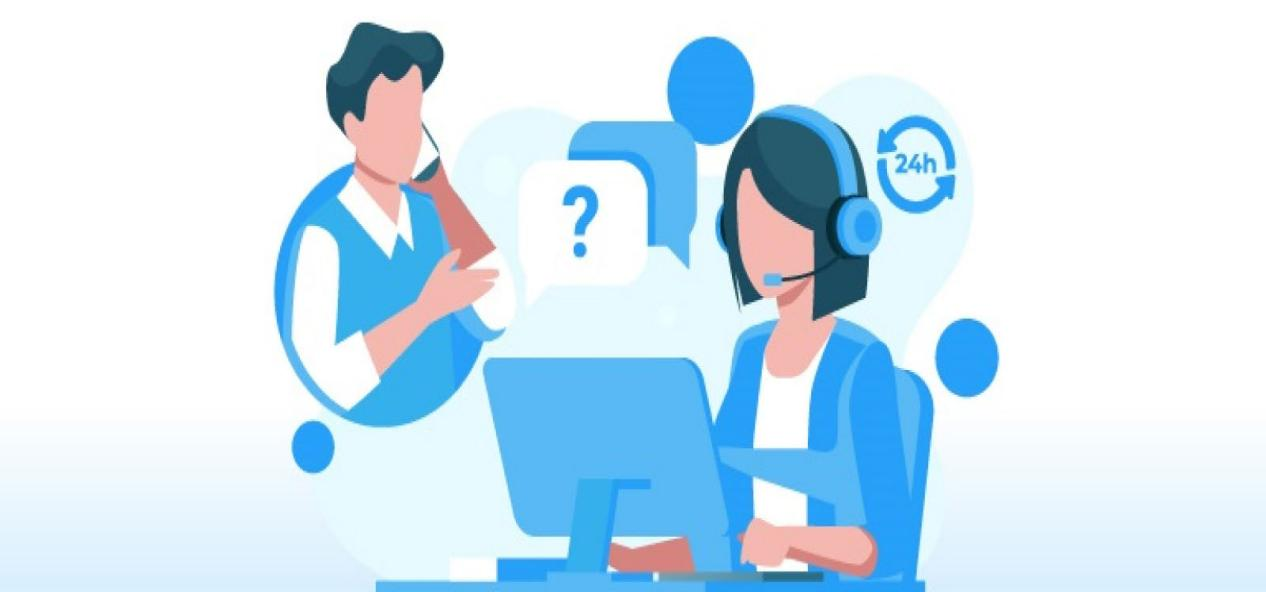
●What is their communication process during the label production and delivery stages?
Clear and timely communication is crucial throughout the label production process. Inquire about the label manufacturer's communication channels and how they keep you informed about the progress of your order. Understanding their communication process ensures that you can stay updated and address any concerns or changes promptly.
●Can they accommodate rush orders or handle unexpected changes?
Business needs can sometimes require quick turnaround times or last-minute changes to label orders. Ask the label manufacturer if they can handle rush orders or accommodate unexpected changes in specifications. Flexibility and responsiveness in such situations are indicators of good customer support.
●What is their return policy in case of defective or incorrect labels?
Despite quality control measures, errors can occasionally occur. Understand the label manufacturer's return policy in case of defective or incorrect labels. Ask about their process for addressing such issues and whether they offer replacements or refunds to ensure customer satisfaction.
By assessing the label manufacturer's customer support services, you can determine their commitment to providing a smooth and satisfactory experience. Consider their communication process, flexibility in handling rush orders or changes, and their return policy for addressing any issues that may arise. Good customer support ensures a positive and successful partnership with the label manufacturer.
Pricing and Payment
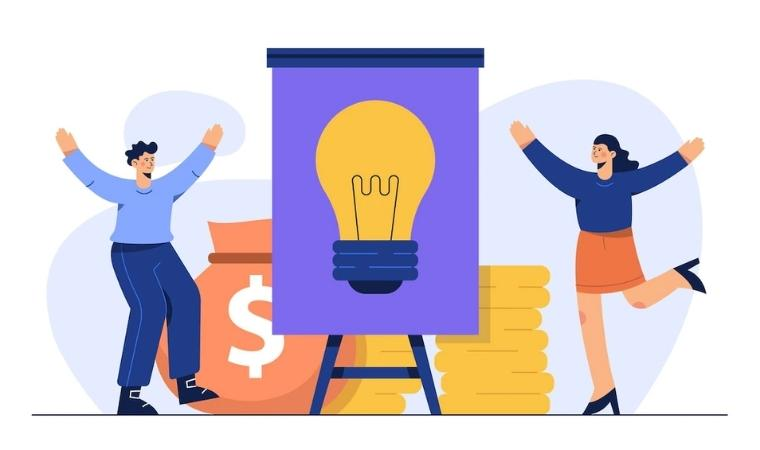
Understanding the pricing structure and payment options offered by a label manufacturer is crucial for budgeting and financial planning. Consider the following aspects when evaluating their pricing and payment terms:
●How do they determine the pricing for label production?
Inquire about the factors that contribute to the overall pricing of label production. This may include considerations such as label size, material, complexity of design, customization options, and order quantity. Understanding their pricing structure will help you assess the cost-effectiveness of their services.
●Do they offer volume discounts or pricing packages for large orders?
If you anticipate placing large orders or require labels on a regular basis, ask the label manufacturer if they provide volume discounts or pricing packages. This can help you save costs over time and establish a long-term partnership that benefits both parties.
●What are their payment terms and methods?
Discuss the label manufacturer's payment terms and methods. Inquire about acceptable payment options, such as credit cards, bank transfers, or payment platforms. Additionally, clarify if they require any upfront deposits or offer any payment flexibility to accommodate your business's financial needs.
●Are there any additional charges or fees to consider?
Sometimes, additional charges or fees may apply outside of the base label production cost. Ask the label manufacturer if there are any additional charges for rush orders, delivery, or any other potential factors. Understanding the full cost breakdown will help you make an accurate assessment of the overall expenses.
By considering the pricing structure, volume discounts, payment terms, and any additional charges, you can make an informed decision about the label manufacturer's affordability and suitability for your budgetary requirements. Clarify any financial aspects in advance to avoid any surprises or misunderstandings down the line.
Conclusion
Selecting the right label manufacturer is crucial for your business. Labels play a vital role in brand promotion, product identification, and information communication.
When evaluating a label manufacturer, consider the following key aspects:
Experience and Expertise: Understanding the manufacturer's experience and expertise helps gauge their industry knowledge and stability. Consider their years in business, specialization, and examples of previous work.
Production Capabilities: Assess the manufacturer's production capabilities, including ability to accommodate different sizes, shapes, and materials, customization options, and production capacity and turnaround time.
Quality Control: Inquire about the manufacturer's quality control measures, customer references, and processes to ensure consistency in color.
Customer Support: Evaluate the manufacturer's customer support services, including communication channels, ability to handle rush orders or changes, and their return policy for defective or incorrect labels.
Pricing and Payment: Understand the manufacturer's pricing structure, volume discounts, payment terms, and any additional charges to determine their affordability and suitability for your budgetary requirements.
By considering these factors, you can make an informed decision and choose a label manufacturer that aligns with your needs, delivers high-quality labels, provides excellent customer support, and offers competitive pricing.
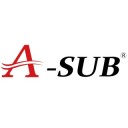